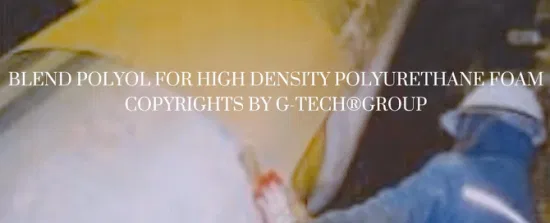
Rigid High Density Open Cell Polyurethane Foam Formulated System Blend Polyether Polyol for Subsea Pipeline Insulation
Overview Package Size 60.00cm * 60.00cm * 102.00cm Package Gross Weight 218.000kg Product Description PRODUCT DESCRIPTIO;
Overview
Feature
• No heat sources are necessary
(process at ambient temperatures)
• Commercially attractive
• Rapid cycle times
• Re-usable or expendable / disposable
(metallic or plastic) mould systems
• Compact, reliable application
equipment
• Compatibility with all conventional
anti-corrosion field joint coating systems
• ODP - zero category formulation
(no ozone damaging CFC solvents)
• Water blown
• No solvents required - all equipment
is air-purged
• A range of foam densitys are available
(6-10 lb / cu ft) typically
Foam Performacne:
Basic Info.
Model NO. | LYR2150A |
Color | Brown |
Dynamic Viscosity (25ºC) MPa.S | 50-150 |
Storage Temperature ºC | 10-25 |
Density (20ºC) G/Ml | 1.1±0.02 |
Hydroxyl Value Mgkoh/G | 350-450 |
Appearance | Light Yellow Transparent Viscous Liquid |
Transport Package | Steel Drum/IBC Drum/Tank |
Specification | pure |
Trademark | G-TECH@ |
Origin | China |
Production Capacity | 50000mt/Year |
Packaging & Delivery
Package Size 60.00cm * 60.00cm * 102.00cm Package Gross Weight 218.000kgProduct Description
Product Description
PRODUCT DESCRIPTION
LYR2150 High Density Polyurethane Foam (HDPF) polyurethane hard foam plastic is used to fill the joints (field joint) of the underground pipeline, to help protect the joints and make the joints with a diameter similar toto easily move through the tube roller tube when sprayed.The material most commonly used by G-TECH is LYR2150. It is a custom-designed high density polyurethane foam (HDPF) with a typical moulded density between 90 kgs per cubic metre (Cellafoam - 150/6) and 160 kgs per cubic metre (Cellafoam - 150/10) un-saturated.Formulated specifically for pipeline field joint applications, the LYR2150 system develops a rigid, open cell structure. Upon immersion, the open cells will absorb water, thereby increasing in overall density to approximately 1025 kgs/m3 (similar to seawater itself).REQUIREMENTS SPECIFICATION- HDPF including two liquid components when mixed together, react within a few seconds turn into solid state and completely filling the joints.
- The components:
- "A": Polymeric isocyanate. An M.D.I., contains Diphenyl Methane-Diisocyanate
- "B": Polyol Blend
- Chemical-Physical:
- Dry density (overall): ≥ 160 kg/m3
- Saturated density (overrall): ≥ 1025 kg/m3
- Compressive strength at 90% deflection: 5.5 MPa
- Open cell content (Free rise core) ASTM D2856 : ≥ 90%
- Viscosity @ 21 0C: 50-150 cps
- Environmennt: CFCs and HCFCs are not allowed
- Response properties:
- Mixing ratio (A:B): 1-1 by volume
- Elongation ASTM D 638: min.5%
- Cream time: /
- Rise time: /
- PACKING REQUIREMENTS:
Feature
• No heat sources are necessary
(process at ambient temperatures)
• Commercially attractive
• Rapid cycle times
• Re-usable or expendable / disposable
(metallic or plastic) mould systems
• Compact, reliable application
equipment
• Compatibility with all conventional
anti-corrosion field joint coating systems
• ODP - zero category formulation
(no ozone damaging CFC solvents)
• Water blown
• No solvents required - all equipment
is air-purged
• A range of foam densitys are available
(6-10 lb / cu ft) typically
Foam Performacne:
Company Profile
You may also like
Send inquiry
Send now